Consumer Durables, High-Tech Industries
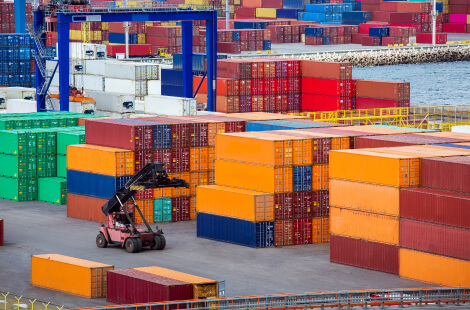

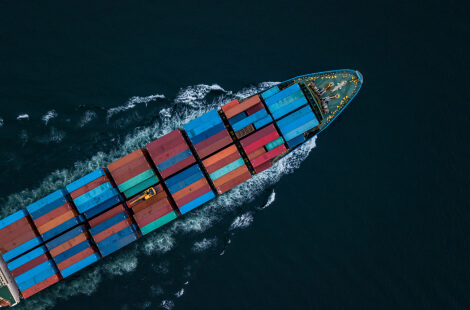

We apply a customized, end-to-end logistics approach to all processes from design to delivery, the management of warehousing and distribution centers, and secondary and last-mile delivery. Our proven expertise in Spare Parts Logistics (SPL) makes us a leader in the category.
Warehousing
- Expertise in Finished Goods (FG) & Spare Parts Logistics (SPL)
- In-plant logistics, fulfilment centres, distribution centre management
- Best-in-class tech solutions for security and loss prevention, customized reporting, real-time visibility, inventory control
- AI based camera analytics solutions for incidence reporting, troubleshooting, and productivity improvement
- WMS enabling multi-channel order management and smart inventory placement
- Returns Management and Insurance Claim Support.
- Security zones for high value inventory
- Efficient storage solutions for high density storage; state-of-the art facilities with pallet rack storage and Material Handling Equipment (MHE) for FMCD FGs
- Customised commercial models including single unit level rate for warehousing & distribution
- Industry leading implementation and transition through leveraging our extensive network and project management capabilities
Transportation
- Pan-India network for omni-channel distribution including B2B and B2C shipments
- Servicing first-mile, middle-mile, and last mile-distribution
- Expertise in full truck load (FTL) and Part Truck Load (PTL) transportation
- Expertise in Designing Milk Run distribution network for optimising cost and managing demand variabilities
- Proven cost-savings, TAT improvement, and minimised damages through innovative Last-Mile Delivery solutions
- Control Tower for real-time visibility and decision-making support to management
Value Added Services
- Demand Planning/ Proactive Inventory Placement
- Flexible solutions to address variability in demand volumes
- Order Fulfilment and Quality Checks for Spare Parts
- Freight Forwarding, Custom Clearance, and Doorstep Delivery
- Sorting, Kitting, Packing, Labelling
- Reduction in handling damages/breakages
- Innovative packaging solutions for cost optimisation
Case Study
How Apollo Supply Chain helped a leading multinational Fast Moving Electrical Good company achieve storage optimization and significant cost savings.
The Challenge
The manufacturing plant was supported by a vast supply chain network with suppliers and distributors located across the country. The manufacturer dealt with high logistics costs accruing from the movements of finished goods between the plant and distributor locations. The challenge faced by the company had the following main features:
Process Overlaps
Two warehouse facilities, located within a distance of 100 km distance, presented the challenges of redundant stoppage nodes and process overlaps.
Low Capacity Utilization
The warehouses lacked multi-tier racking systems, as a result of which pallets were stored mostly on the warehouse floor. This resulted in low storage utilization.
Higher Logistics Cost
Inefficient production planning and demand forecasting methods resulted in the mismanagement of inventory handling, adding further to the total logistics cost.
The Solution
Rationalization
The supply chain network design needed to be rejigged. The origin-destination pairs, for example, needed to be rationalized taking their respective distances from warehouses into account.
Better-Suited Configuration
The Apollo Supply Chain team implemented a mix of ground and rack storage configuration to improve utilization and reduce costs.
Warehousing Process Optimization
The team improved and optimized warehousing processes at three warehouses located across North India, which together handled nearly 0.05 million SKUs.
Warehouse Consolidation
The total number of warehouses needed to be consolidated to optimize resource utilization and compliance costs in line with local and national regulations.
Warehouse Relocation
Efficient transfer planning resulted in relocation of an existing warehouse within a week’s time.
Reduced COG
A reduced cost of goods (COG) was obtained through improved network optimization and warehouse consolidation based on a study that helped in saving the in-transit cost.
The Result
Improved Cost-Efficiencies
Capacity Improvement
The annual tonne-km by 29 percent
Reduced Transport Cost
The transportation cost by nearly 7 percent
Optimized warehouse space
Reduced warehousing area by 26 percent